Through its subsidiary ICMD Holding GmbH, HMT is currently implementing a number of construction projects for the production of an innovative ferro-silicon-aluminum alloy. Since 2012, ICMD Holding GmbH holds an exclusive license for the production of this alloy, as well as a patent holder for the production technology of high-purity ferro-silicon. Through ICMD Holding GmbH accompanies the HMT Group projects for the construction of ferro-alloy plants in Kazakhstan – KCAP LLP, Kyrgyzstan – Avinien LLC, in Brazil – General Alloys Ltda. for the production of ferro-silicon-aluminium.
The primary goal of establishing the ICMD was organization of the industrial production of ferro-silicon-aluminum alloy, as well as other complex alloys in Kazakhstan, Kyrgyzstan and other countries; and their distribution, participation in the development of new technologies for the production of alloys FeSi75 with low aluminium content from unconventional raw materials, production of chromium nickel cast iron for the production of stainless steel brands, production of low carbon ferromanganese from complex iron ores.
In 2011, ICMD launched series production of ferro-silicon-aluminium at the Ekibastuz Mini Smelter A and K LLP. The project capacity of this mini smelter was 3,000 tons per year, the alloy produced was delivered to the Russian and Japanese steel mills for processing of killed and semi-killed steel brands. Between 2011 and 2012, more than 5,000 tons of FeSiAl were produced.
At the beginning of 2013, the ferro-silicon-aluminium production was developed in three SAFs of 9 MVA (1 furnace) and 24 MVA (2 furnaces) at KSP Steel (Pavlodar) under a sublicensing agreement. The total output of the three furnaces reached 24,000 tons per year.
In total, about 50,000 tons of alloy were sold to the metallurgy companies in Kazakhstan (AO ArcelorMittal Temirtau), Russia (Magnitogorsk MK, Omutninsk MK, ZAO Ferrosplav and others), Germany (Thyssenkrupp steelworks), Korea (POSCO), Japan (Kobe Steel, JFE Steel Corp.), China (Baosteel).
Karaganda Complex Alloys Plant, Karaganda, Kazakhstan
To date preliminary construction works are completed for erection of a complex alloys plant with annual capacity of 90 thousand tons with 4×33 MVA furnaces. It is envisaged to produce not only ferro-silicon-aluminum, but also ferro-silicon and ferro-silicon-manganese.
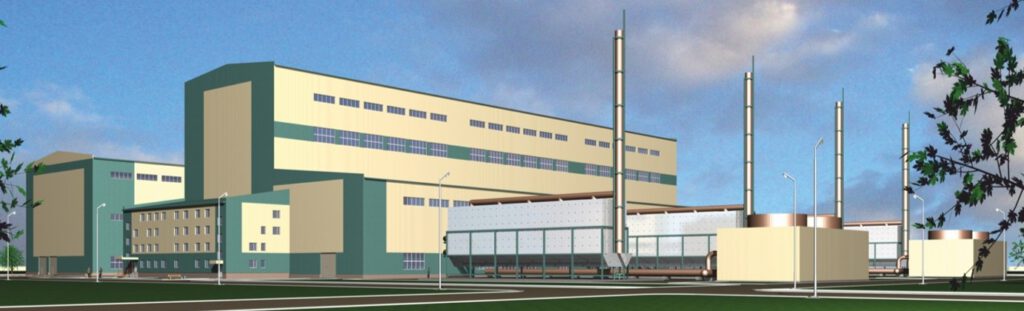
Avinien LLC, Tash-Kumyr, Kyrgyzstan
The construction of the ferroalloy plant with capacity of 50 000 tons per year of FeSiAl alloy in the Kyrgyz Republic was launched in 2014.
Avinien LLC shareholders are: Republican State Enterprise National center on complex processing of mineral raw materials of the Republic of Kazakhstan and ICMD International Corporation of Metal and Alloy Development Holding GmbH, Germany.
Due to the electric power deficit in 2016 caused by political and economic crisis in the country the construction was suspended. At present negotiations are being conducted with the Government of the Kyrgyz Republic to secure guaranteed volumes of the electric power and to resume the construction of the plant.
General Alloys Importação e Exportação Ltda., Sao Paulo, Brazil
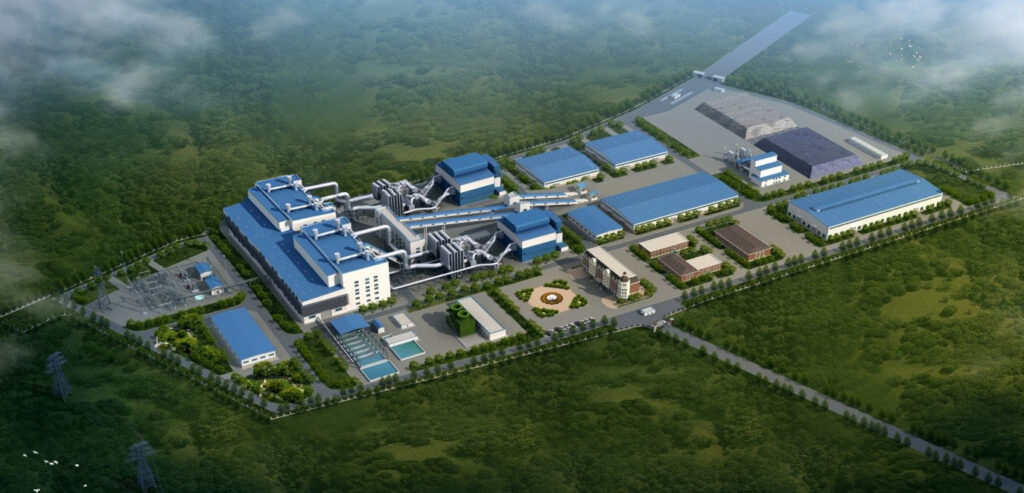
2012 in the state Minas Gerais, a 12 MVA furnace was rented with a further buy out option, where it was envisaged to organize the production of ferro-silicon-aluminum. However, due to the energy crisis in Brazil in 2014 and the following years and the repeated skyrocketing of electricity prices (4-8 times), a decision was made to freeze this project because this situation with electricity deficit and high prices still exists in the State Minas Gerais.
In that regard ICMD Holding GmbH has decided to reorient its operations to the coal state Santa Catharina, where energy tariffs are more acceptable. A business plan has been developed for the construction of a FeSiAl smelter with a total annual capacity of 72 thousand tons in 4 furnaces. Negotiations are underway with coal and energy companies, as well as with the city hall of Chriciuma on the provision of land for the construction of the smelter.
Ferro-Silicon-Aluminum Alloy (FeSiAl)
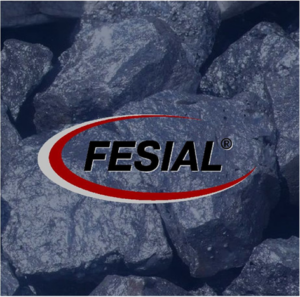
Traditionally in steel making the melt is deoxidizing by the combined use of secondary aluminum and ferro-silicon. The newly developed Ferro-Silicon-Aluminum combines the metallurgical properties of aluminum as well as ferro-silicon and can therefore be used as substitution product for deoxidation. The metallurgical benefit of the new alloy has already been tested at several renowned mills and all test results accessible to us proved that the use of standard ferro-silicon could be fully substituted and that the use of aluminum can be considerably reduced by using this alloy.
The technology of ferro-silicon-aluminum smelting from high-ash coal and dump high-ash carbonaceous rocks developed by Kazakhstani scientists has high technical and economic indicators, where the use of expensive coke is completely excluded. The technology is protected by international patents.
Ferro-silicon-aluminum (FeSiAl) alloy represents complex silicon-aluminum alloys. A distinctive feature of the technology of carbothermal production of FeSiAl is the ability to smelt an alloy with a silicon content of 40-70% and aluminum 10-25%.
FeSiAl grades FeSi45Аl10, FeSi45Аl15, FeSi45Аl20 and FeSi55Аl15 successfully replace traditional Ferro-silicon FeSi65 and FeSi75, as well as secondary aluminum of the AB80 and AB85 grades when processing low-grade and low-alloyed steels. If Ferro-silicon does not contain any special harmful impurities except phosphorus, the content of which is limited, the secondary aluminum of the AB80-85 grades contain significant amounts of non-ferrous metal impurities (zinc, lead, copper, etc.) which significantly affect the quality of the steel and refractory lining of electric arc furnaces and ladles.
Numerous industrial tests of FeSiAl in steel processing showed a significant improvement of the quality while reducing the cost of steel production by increasing the beneficial use of silicon and aluminum, in contrast to the traditional scheme of separate deoxidation of steel with ferro-silicon and aluminum. The increase in the beneficial use of aluminum in the composition of FeSiAl is explained by the presence of intermetallic phases of silicon and iron, as well as iron and aluminum.
When interacting with the steel melt the aluminum in the composition of the FeSiAl is screened from oxidation by silicon, which first begins to interact with iron oxide (FeO), and only after this does the dissolved oxygen interact with the aluminum. Such a mechanism of steel deoxidation when using FeSiAl allows increasing the useful use of aluminum and significantly reducing the frenzy of aluminum. The resulting oxide deoxidation products in the steel volume have a complex composition ([Fe, Mn] O • SiO2, Al2O3), which contributes to their low melting point and easier and complete removal from the steel volume.
A reduction in the amount of residual non-metallic inclusions by 1.5-2 times was achieved in contrast to the traditional deoxidation method. At the same time, residual non-metallic inclusions are characterized by fine dispersion and uniform distribution throughout the steel with favourable morphology.
At the stage of industrial research tests were conducted in large metallurgical companies:
- thyssenkrupp AG(Germany)
- POSCO (South Korea)
- Çolakoğlu Metalurji A. Ș. (Turkey)
- JFE Steel Corp. (Japan)
- KobeSteelLtd. (Japan)
- «Arcelor Mittal Temirtau» JSC (Republic of Kazakhstan)
- «KazChrome» JSC (Republic of Kazakhstan)
- Omutninsk Metallurgical Plant JSC (Russian Federation)
- Magnitogorsk Iron and Steel Works JSC (Russian Federation)
After successful testing of the alloy at the metallurgical enterprises in the CIS countries and abroad, agreements were reached on regular deliveries of products after the resumption of FeSiAl production to enterprises: ArcelorMittal Temirtau (Kazakhstan), NLMK, ММК, and ОМК (all – Russia), POSCO Group (South Korea), China Baowu Steel Group (former Baosteel Group Corporation, China). In addition, an off-take agreement was concluded with thyssenkrupp Materials Trading (Germany) and a distribution agreement was signed with the HANWA Group (Japan).
According to the tests results and marketing research thyssenkrupp AG concern (29th place in the world, table 2.14) expressed its opinion on ferro-silicon-aluminum: „We hereby confirm that we have the rights to market an innovative alloy of ferro-silicon-aluminum which is in our opinion, a key event in the development of metallurgy.“
Another major application of FeSiAl is its use as a reducing agent for production of refined grades of ferro-chrome and ferro-manganese, as well as in the production of a number of other alloys and master alloys instead of ferrosilicon-chrome and ferrosilicon-manganese with the addition of lime, which contributes to the scattering of the final slags into fine powder during cooling. The use of FeSiAl reduces by 35-40% the addition of lime, 20% power consumption, respectively, the slag ratio from 3.0-4.0 to 1.8-2.5, eliminating the crystallization of two-calcium silicate, thereby, the tendency to slaking.
The use of FeSiAl in the smelting of refined ferro-chrome varieties at the Aktobe ferroalloy plant has shown that it is possible to reduce the cost of production of ferro-chrome by 300-350 USD.
Ferro-silicon-aluminum exhibits a higher deoxidizing ability in comparison to use of ferro-silicon and aluminum. Thus, the replacement of these products with ferro-silicon-aluminum significantly reduces the consumption of raw materials and consequently reduces the cost. Since the modern global steel market is highly consolidated and aimed at improving efficiency, the use of ferro-silicon-aluminum will allow manufacturers to significantly reduce costs and thus increase their profits.
Further positive side effects of using the alloy are expressed in a more thorough decontamination of the smelt from non-metallic inclusions and in improved quality of the steel surface (less cracks).
From the manufacturer’s point of view, ferro-silicon-aluminum is a highly effective product. In addition to the electricity required for the production of all alloys, the production of standard ferro-silicon and aluminum includes the use of several expensive materials (for example quartzite, alumina and reducing agents). In contrast ferro-silicon-aluminum is produced primarily from low-grade coal.
Unlike secondary aluminum there are no non-ferrous metal impurities in the composition of FeSiAl, and the cost per unit of aluminum is 1.5-2 times lower than in pure electrolytic aluminum.
The distinctive feature of the new technology is the use of high-ash carbonaceous raw materials, which is a ready-made natural briquette (mono-mix), where favourable combinations contain compounds of silicon and and solid carbon the amount of which is sufficient for reduction processes and coke addition are not required.
Raw materials costs for smelting FeSiAl are over 50% lower, than those for FeSi75 only due to use of sub-standard raw materials which traditionally go to dumps. And cost of production of FeSiAl is 25 – 35% lower in comparison to cost of production of FeSi75.
The chosen technology for the production of ferro-silicon-aluminum is currently the most effective and beneficial in terms of technology and economics. The basing of technology on the use of high-ash carbonaceous raw materials related to industrial wastes as well as its large reserves open up great prospects for the production of complex silicon-aluminum alloys.
The new technology makes it possible to produce a whole group of complex alloys based on ferro-silicon-aluminum with the addition of alloying elements (vanadium, boron, rare earth metals) and non-metal inclusions modifiers (calcium, barium, strontium).